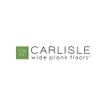
Carlisle Regur Wood Flooring
REGUR WOOD FLOORING
REGUR WOOD FLOORING
Typically found in the lava covered valleys surrounding a volcano, Regur is partly born of fire. Gray is typically considered a cooler color but with the brown tones of the Hickory heartwood pushing to the surface Regur creates the warmth imagined in slowly flowing lava.
With hints of black in the more open grain, creating a touch of the dramatic, this floor will be a supportive statement piece to all the architectural elements in your home.
INFORMATION
BRAND
Carlisle
PRODUCT TYPE
Flooring
COLLECTION
Regur
STRUCTURE
Solid or Engineered
GRADE
- Heirloom
- Original
- Signature
ATTIC STOCK
-Order quantity requires that 10% above the actual coverage SF be included in the quantity requested. -It is recommended that an additional 5% be added to the order to provide the customer with attic stock for future unexpected repairs
TEXTURE
- Smooth
- Timeworn
- Brushed
- Footworn
- Hand Scraped Edge
FINISH
Extra Matte
USE
Indoor
MANUFACTURING PROCESS
- Product must be made in the USA
- Hot glue process for engineered structure
- Multi-point individual board press laminating process
SOLID WOOD FLOORING
-Product must be made in the USA -Moisture content should be in the 6-9% range -Milling tolerance must meet or exceed NWFA Standards -Relief grooves 3/8” deep, every ¾” across the bottom of the planks
ENGINEERED WOOD FLOORING
-9-11 Layers-Plywood substrate -Hardwood wear layer dry sawn veneer -California Air Resource Board (CARB2) compliant -Moisture content of wear layer at time of manufacture may be from 6-9% -Wear layer thickness of 4mm nominal (specified textures and finishing process may slightly alter finished thickness)
DETAIL
-HVAC system must be in place and operational maintaining temperatures between 60-80° degrees F (16-27° C) and relative humidity of 30-55% for at least 14 days prior to the start of acclimation. -Building envelope must be closed in and weather tight, with painting complete except for final coat on trim detail that may impact the flooring installation. All concrete, plaster, tile and other “wet work” has been completed and is no longer contributing moisture to the environment such that the environment is outside normal living conditions. -To the extent that exterior grade may impact the moisture content of the substrate structure all grading should be pitched away from structure and any necessary downspouts and gutters should be installed..
INSTALLATION
An experienced installer who has completed wide plank flooring installations with a determined record of successful in-service performance. Our Earthen Collection offers both Engineered and Solid Structures.
DELIVERY, STORAGE AND HANDLING
-Forklift accessible crates -Deliver material in moisture protective wrapping -Planks are stacked in custom crates to accommodate the long board lengths. Crate dimensions are roughly 192”L x 44”W x 30”H, depending on the square footage. -Protect flooring from exposure to moisture. DO NOT deliver flooring until all concrete, plaster, tile and other “wet work” has been completed and is no longer contributing moisture to the environment such that the environment is outside normal living conditions. -Flooring must be acclimated to a controlled environment, replicating near live-in conditions, 5-7 days prior to installation. Accurate length of time must be determined by the installer.
MATERIAL
- Hickory
- Extra Matte sheen 6-9°
- T and G edge joints and end matched
- NWFA/NOFMA Certified Manufacturer
- 8” wide planks, 2’-12’ lengths with 6’-7’ average
- Engineered or Solid Flooring is 3/4” total thickness
- Softened edge on the 2 long sides of each plank of 1/32” - ENDS ARE NOT EASED
- Grade of material is a proprietary grade created by Carlisle. Wood Filler not allowed on the surface of the planks.
SUBFLOOR REQUIREMENTS
-Subfloor must be flat. Level and flat to within 3/16” in 10’. Check with your installer with regard to specific requirements that intended underlayment and/or adhesives may require that are different than this specification. -Floor must have all loose debris, paint, drywall material or other material removed that may impact appropriate adhesion of the flooring material to the substrate structure. -Concrete substrates must be dry. Dryness of substrate must be measured and documented (photographed), and dated using appropriate testing methods. Relative Humidity testing (ASTM F2170) must not exceed 75%. Calcium Chloride testing (ASTM F1869) must not exceed 3lbs of moisture emission per 1000sf over a 24 hour period. -Wood subfloors are not to exceed 12% and should be within 2% of the moisture content of the flooring material prior to starting installation, when sampled using an appropriate resistance (pin-type) meter.
COLORS
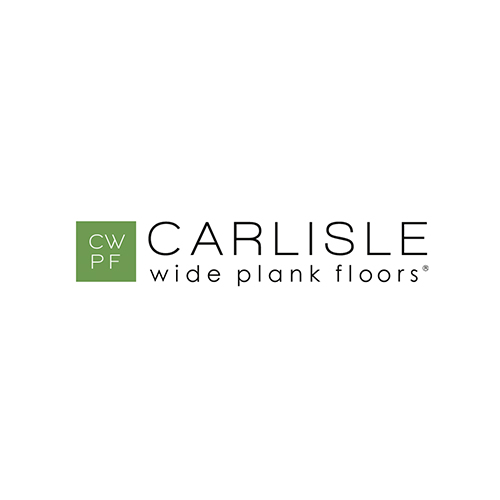