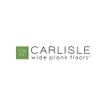
Carlisle Crossroads Flooring
CROSSROADS FLOORING
CROSSROADS FLOORING
Named for the enticing mystery of life’s crossroads, this floor shrouds the White Oak with a gentle gray haze that deepens to highlight grainlines.
INFORMATION
BRAND
Carlisle
PRODUCT TYPE
Flooring
INSTALLATION
- Plywood
- Residential
- Commercial
- Radiant Heat
- Concrete Slab
- Waterfront
ENGINEERED WOOD FLOORING
-9-11 Layers-Plywood substrate -Hardwood wear layer dry sawn veneer -California Air Resource Board (CARB2) compliant -Moisture content of wear layer at time of manufacture may be from 6-9% -Wear layer thickness of 4mm nominal (specified textures and finishing process may slightly alter finished thickness)
FINISH
Prefinished
EDGE
Softened
TEXTURE
Smooth
USE
Indoor
STRUCTURE
- Solid
- Engineered
GRADE
- Heirloom
- Signature
PROFILE
Tongue & Groove
MINIMUM ORDER
800 SQ FT
DETAIL
The natural color of the wood is visible beneath the gray wash, creating a hue that is best described as “greige.” The result is a wonderful neutral floor that is both peaceful and eye-catching.
SURFACE
Wood subfloors that allow for nailing (at industry prescribed schedule) require at minimum; the use of a caulking gun (such as Wakol MS 265) adhesive bead, applied across the full width of the planks at intervals of 8-12” in addition to mechanical fastening. Full-spread wood flooring adhesive applied by trowel to the substrate surface is recommended and will provide the most optimal method of glue-assist.
MANUFACTURING PROCESS
- Product must be made in the USA
- Hot glue process for engineered structure
- Multi-point individual board press laminating process
SOLID WOOD FLOORING
- Moisture content should be in the 6-9% range
- Milling tolerance must meet or exceed NWFA Standards
- Relief grooves 3/8” deep, every ¾” across the bottom of the planks
INSTALLER QUALIFICATION
An experienced installer who has completed wide plank flooring installations with a determined record of successful in-service performance. Our Explore Collection offers both Engineered and Solid Structures.
MATERIAL
- White Oak
- Naturals / Super Matte sheen 2-4°
- T and G edge joints and end matched
- NWFA/NOFMA Certified Manufacturer
- 8” wide planks, 2’-12’ lengths with 6’-7’ average
- Engineered or Solid Flooring is 3/4” total thickness
- Softened edge on the 2 long sides of each plank of 1/32” - ends are not ease
- Grade of material is a proprietary grade created by Carlisle. Wood Filler not allowed on the surface of the planks.
DETAIL
-Flooring should be installed in the direction recommended by the Architect or Designer or parallel to the longest wall. -Expansion space of at least ½” is required around the perimeter of the installation in each room. -Installation using full-spread glue requires the of use appropriate surface weight to properly set the individual board into the adhesive.
Adhesive transfer of 95% or more to the bottom of the plank is required and must retain contact with the adhesive and substrate once dry and cured. 5 gallon buckets filled with sand or water are most commonly used for this purpose. Depending on adhesive requirement weights can typically be redistributed after 20 minutes. -Depending on subfloor conditions and nature of the adhesive the use of shims may be required to ensure flush edge and end joint configuration.
SUBFLOOR REQUIREMENT
-Subfloor must be flat. Level and flat to within 3/16” in 10’. Check with your installer with regard to specific requirements that intended underlayment and/or adhesives may require that are different than this specification. -Floor must have all loose debris, paint, drywall material or other material removed that may impact appropriate adhesion of the flooring material to the substrate structure.
-Concrete substrates must be dry. Dryness of substrate must be measured and documented (photographed), and dated using appropriate testing methods. Relative Humidity testing (ASTM F2170) must not exceed 75%. Calcium Chloride testing (ASTM F1869) must not exceed 3lbs of moisture emission per 1000sf over a 24 hour period. -Wood subfloors are not to exceed 12% and should be within 2% of the moisture content of the flooring material prior to starting installation, when sampled using an appropriate resistance (pin-type) meter.
COLORS
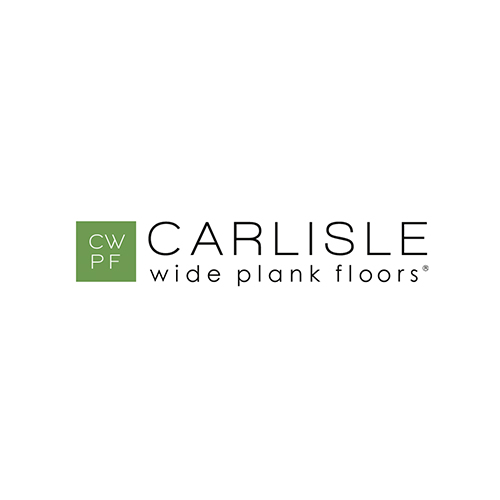